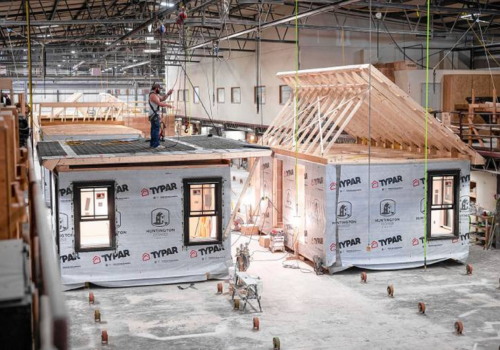
In a large factory in East Montpelier, Vermont, houses are being built piece by piece on an assembly line—a process that could help address the state's severe housing shortage.
At Huntington Homes, co-owner Jason Webster describes their modular homes as “Lego blocks.” These homes start as simple structures in a 100,000-square-foot facility, where they are gradually built with floors, walls, ceilings, wiring, insulation, and paint. Unlike traditional construction, which requires coordinating multiple subcontractors on-site, this method allows all tradespeople to work under one roof, streamlining the process and reducing build time.
“We can build a whole house in 12 eight-hour shifts — so, 96 hours,” Webster said.
Once completed, these modular homes are transported to their final destinations, where they are assembled by crane. To the average observer, they are indistinguishable from conventionally built houses. Huntington Homes constructs about 70 such homes each year.
Vermont’s Housing Shortage and the Role of Modular Construction
Vermont is struggling to meet its housing needs. Last year, only around 2,000 homes were built—just a quarter of what experts estimate is necessary for a stable housing market. The state has yet to recover from the 2008 housing market crash, which significantly slowed home construction.
With the demand for housing growing, policymakers are looking at modular construction as a potential solution. A recent state-commissioned report explores ways to expand Vermont’s off-site construction industry, which includes both modular homes and manufactured housing.
“The hyperscale data centre market is rapidly expanding, and Gleeds is well-positioned to capitalise on this growth,” said Stuart Lumsden, US CEO.
Advantages of Factory-Built Homes
Modular construction offers several benefits, including:
Year-Round Building
Vermont’s harsh winters often slow traditional home construction. Factory-based construction allows homes to be built regardless of the season.
Lower Costs
Producing homes in a factory reduces material waste and takes advantage of economies of scale. "If we build one home at a time — a home here, a home there — then, it’s about the least efficient way that you can do anything, right?” said Jeff Lubell, a housing researcher involved in the Vermont report.
Workforce Accessibility
Factory-based construction is less physically demanding than traditional building, which could attract a broader range of workers in a state struggling with labor shortages.
Faster Production
Instead of taking months to build a home, modular construction can complete homes in days.
Challenges and Considerations
Despite the promise of modular housing, challenges remain. Establishing a factory requires significant upfront investment, making it vulnerable to economic downturns. A recession can force an entire factory to close, unlike traditional homebuilders who can scale down operations.
This was the fate of Vermont’s Fair Haven plant, which shut down in 2011 after the 2008 housing crash reduced demand for manufactured homes. The number of modular home factories in New England has significantly declined since then.
Housing Commissioner Alex Farrell acknowledges the risks: “We, the state, need to be thinking about that eventual bust cycle. We’re here to mitigate risk for the public and then for private developers, but we just don’t want to leave the state holding the bag.”
Potential State Involvement in Modular Housing
To mitigate these risks, the state report suggests strategies such as bulk purchase agreements, where the government commits to buying a set number of factory-built homes. Some developers, like Summit Properties, are already using this model. The company recently purchased 45 modular duplexes and townhomes from Huntington Homes for a mixed-income development in Middlebury.
“It boils down to cost,” said Zeke Davisson, Summit’s chief operating officer. By choosing modular construction, Summit expects to save “up to 10%” on construction costs.
Another proposal is reopening defunct manufacturing plants, such as the former Skyline factory in Fair Haven. With state funding, the facility could potentially resume operations, providing affordable housing while also creating jobs.
A Path Forward for Vermont
As Vermont continues to grapple with a severe housing crisis, modular construction presents a viable path to increasing housing supply quickly and affordably. While concerns about economic downturns remain, housing experts argue that the potential benefits outweigh the risks.
“To Lubell, the housing researcher, putting a relatively small amount of state money toward off-site construction poses a low risk compared to the status quo: watching as housing prices continue to rise.”
The smartest construction companies in the industry already get their news from us.
If you want to be on the winning team, you need to know what they know.
Our library of marketing materials is tailored to help construction firms like yours. Use it to benchmark your performance, identify opportunities, stay up-to-date on trends, and make strategic business decisions.
Join Our Community