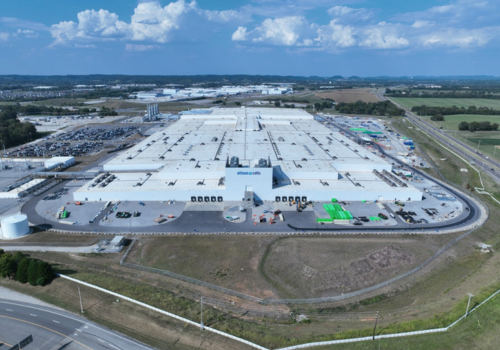
From Tennessee to Michigan, GM Expands Battery Innovation for an Electric Future
Just outside Nashville, in the hills of Spring Hill, Tennessee, General Motors and its joint venture partner LG Energy Solution are driving the next wave of American battery technology through Ultium Cells — now the largest OEM battery cell manufacturing capacity in the country with sites in Spring Hill and Warren, Ohio.
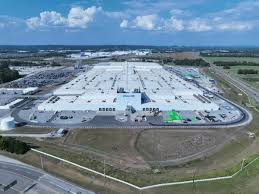
Building on a $2.3 billion commitment made in 2021, Ultium Cells Spring Hill is now at the center of GM’s strategy to produce multiple advanced battery chemistries. Alongside its nickel cobalt manganese aluminum (NCMA) pouch cells, the plant will soon add lines for lithium iron phosphate (LFP) battery cells — an American innovation that has become a global low-cost solution for EV batteries.
“I’m proud that we’re bringing its benefits — and associated jobs — back to America,” GM said in its announcement. Work on the new LFP cell lines will start soon, with full production expected by late 2027.
Spring Hill will anchor LFP production, but GM isn’t stopping there. The automaker recently announced plans to become the first to produce lithium manganese rich (LMR) prismatic battery cells at commercial scale — an advancement seen as crucial to balancing range, performance, and affordability across its EV lineup.
GM’s push into three battery chemistries — NMCA, LFP, and LMR — aims to expand its capacity to build both premium electric pickups and more affordable EVs like the Chevrolet Bolt, giving customers more choices while driving down costs.
Meanwhile, in Michigan, progress continues at GM’s Warren campus, where the final steel beam was recently installed at the newly named Ancker-Johnson Battery Cell Development Center. Together with the Wallace Battery Cell Innovation Center next door, GM has invested $900 million at its nearly 70-year-old Global Technical Center to strengthen its U.S. tech base.
The Ancker-Johnson Center — named for pioneering physicist and former GM executive Betsey Ancker-Johnson — is designed to cut new battery development timelines by as much as a year. Its first major assignment? Fast-tracking LMR batteries to market ahead of the competition.
Development teams at the new 500,000-square-foot complex will focus on validating new cell concepts and preparing them for large-scale production, helping GM keep pace in the global race for battery leadership.
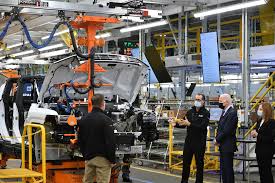
“These investments reinforce our commitment to build a resilient, U.S.-based EV material supply chain,” GM said. Recent strategic agreements include securing U.S.-sourced lithium and magnets to support long-term growth.
From new chemistries to next-generation facilities, GM says every step is about building a robust, American-led EV portfolio: “We think we’re in a better position than any other automaker to lead the industry, and the country, on this road to the future.
GM’s battery push extends beyond new chemistries and factories. The company has secured supply chain deals for critical minerals and invested in domestic mining partnerships, aiming to insulate its EV growth from global raw material volatility.
Its Spring Hill facility will play a pivotal role in scaling LFP cell production for affordable EVs — technology that has already gained traction in markets like China due to its lower cost and stable supply. By producing LFP in the U.S., GM hopes to localize manufacturing and create thousands of skilled jobs while staying competitive in price-sensitive segments.
At the same time, the Ancker-Johnson Center in Warren, Michigan, will advance next-gen battery designs that promise higher energy density and faster charging. Teams there will test and validate cells that could unlock longer driving ranges and better performance for future electric trucks, SUVs, and fleet vehicles.
The Warren campus also serves as a training ground for future battery engineers and technicians, with partnerships that connect local talent to the emerging EV workforce pipeline.
Combined with its growing Ultium Cells footprint, GM’s investments in Tennessee and Michigan underscore its bet that an American-made battery supply chain is key to meeting consumer demand, driving down EV costs, and competing globally.
Industry analysts say these moves strengthen GM’s claim to be a leader in the fast-changing battery race — a race where speed, scale, and supply chain control may decide who stays ahead as the EV market matures.
Originally reported by Mark Reuss in GM Motors.
The smartest construction companies in the industry already get their news from us.
If you want to be on the winning team, you need to know what they know.
Our library of marketing materials is tailored to help construction firms like yours. Use it to benchmark your performance, identify opportunities, stay up-to-date on trends, and make strategic business decisions.
Join Our Community