Maine Housing Leaders Advocate for Modular Construction to Tackle Shortage
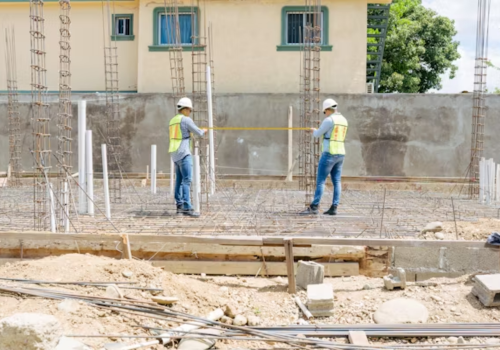
Maine’s largest modular construction company is contributing to solving the state’s housing crisis by offering faster, high-quality construction methods.
PARIS, Maine — Walking through KBS Builders’ plant in South Paris is no small feat, as the busy production floor echoes with the sounds of construction: saws, nail guns, and the rhythmic sound of materials being moved around the space.
With 112 employees, KBS Builders constructs both residential and commercial buildings in this vast indoor area, sheltered from the harsh winter weather and seasonal elements. This indoor environment allows for year-round production, ensuring efficiency regardless of the unpredictable Maine weather.
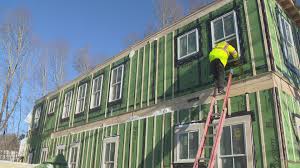
As the state grapples with a serious housing shortage, state housing leaders are increasingly turning to modular construction for solutions. KBS, being Maine’s largest modular builder, is in the spotlight as they push for faster and more cost-effective ways to meet growing housing demands.
“I think modular is the answer to affordable housing,” said KBS President Thatcher Butcher. “If we add more supply into the equation, it will bring prices down. When we talk about affordable housing, the only way to get there is to increase the supply.”
State officials are beginning to view modular construction as a means of rapidly expanding housing availability. Maine Housing, formerly the Maine State Housing Authority, has financed two multi-family modular projects: an 18-unit development in Madison that opened in early 2024, and a 16-unit project in Newcastle that is currently under construction. Both projects have seen accelerated construction timelines, thanks to modular techniques.
Maine Housing Executive Director Dan Brennan is optimistic about these developments. He noted that traditional multi-family construction usually takes a year to 18 months to complete. By contrast, the Madison modular project broke ground in October 2023 and opened in the spring of 2024—just six months later.
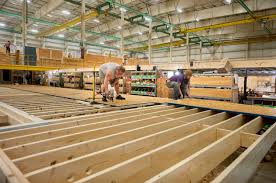
“There is definitely an opportunity to scale up that kind of construction,” Brennan remarked in a recent interview. “I know there are discussions with [the] Governor’s office, DECD (Department of Economic and Community Development), and others looking to entice the company to set up another facility."
Butcher highlighted how KBS has managed to streamline construction over recent years. Today, the average project takes just two weeks to build inside the factory.
The modular assembly process resembles an assembly line. The first step involves placing pieces of lumber onto a raised table to form the floor unit for the housing module. The lumber is cut with precision by a CNC saw, which also drills holes for plumbing pipes and wiring.
The CNC saw ensures accuracy by printing a unique numbered code on each piece, helping workers easily identify where each component belongs in the overall construction. Once the parts are aligned, they are nailed together, and plywood is added to complete the floor section.
“Framing exterior walls with dimension lumber [is the] same as you might see in an on-site house,” Butcher explained.
He praised the advancements in modular construction quality, noting, “Ten to fifteen years ago a site-built building would have had higher quality than a modular product. Now, the product we are building far exceeds something you would get on site.”
Building in a controlled indoor environment enables KBS to achieve higher quality control and energy efficiency compared to traditional construction.
As floor sections are assembled, any necessary plumbing and wiring are installed beneath the units, and temporary wheels are attached so the units can move easily across the factory floor. As the construction progresses, walls are added, insulation is installed, and finishes like sheetrock, doors, windows, and flooring are incorporated.
The completed units leave the factory with their interiors mostly finished and their exteriors ready for siding. The roof panels are already attached and can be hoisted into place by a crane at the construction site.
On average, KBS completes two units daily, which are then transported to construction sites for final assembly.
While the cost of modular construction isn't necessarily cheaper than conventional building, Butcher emphasizes that the major advantage is the speed of construction, which allows for greater efficiency in delivering new housing.
For Maine Housing, the ability to quickly add more housing units is a major selling point.
With demand for modular construction growing, Butcher revealed that KBS has already secured another building just a few miles from their current facility. This new space is slated to become a second manufacturing plant, further expanding the company’s capacity to meet the rising demand for modular housing.
This push towards modular construction reflects a larger trend within Maine as the state continues to search for innovative solutions to address its housing shortage.
Originally reported by Don Carrigan in News Center MAINE.
The smartest construction companies in the industry already get their news from us.
If you want to be on the winning team, you need to know what they know.
Our library of marketing materials is tailored to help construction firms like yours. Use it to benchmark your performance, identify opportunities, stay up-to-date on trends, and make strategic business decisions.
Join Our Community