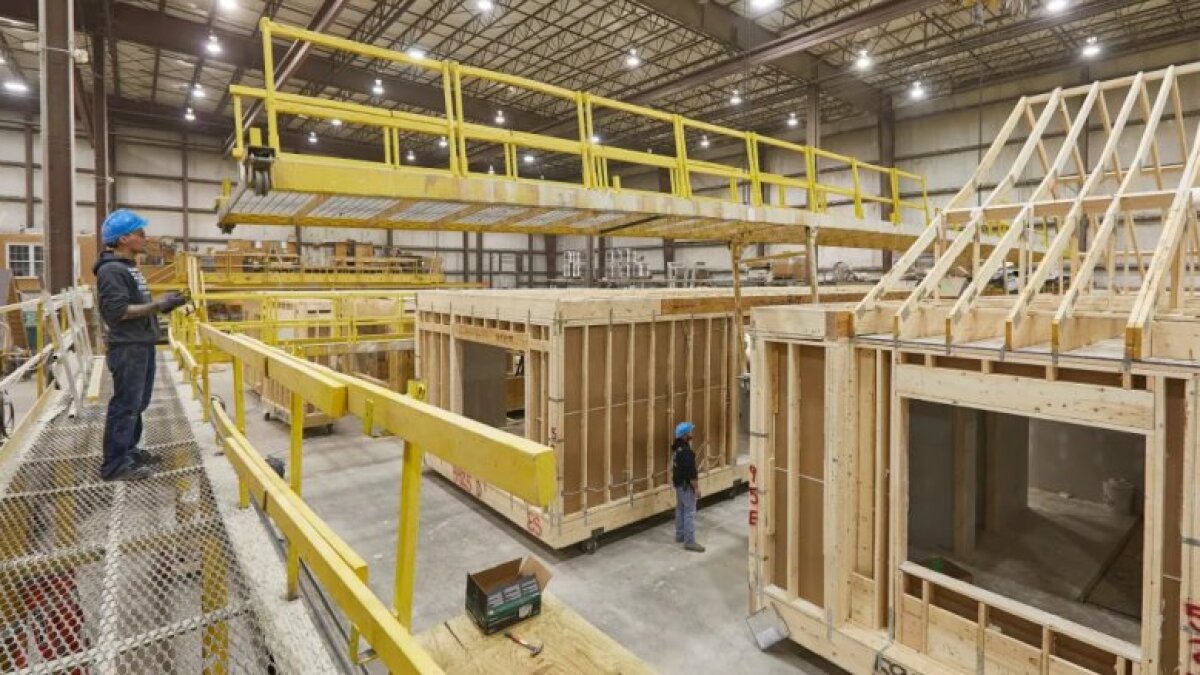
When you meet folks behind many of the offsite home building companies, you find them teeming with passion. Even though they can make housing faster than anyone else, that passion isn’t capitalism. It’s passion for solving global issues.
Many of them are dedicating their life’s work to trying to solve for the housing affordability crisis with a unique approach to manufacturing, design or automation that can lower costs.
Here are several and what they are doing to change the economies of housing at the same time they are changing humanity.
Assembly Line
In March this year I was at the SXSW conference in Austin and saw that Juno was offering a tour of a new multifamily housing development to show off its offsite productization approach.
With a broad mission to provide for healthier communities, cities and planet, Juno uses component- and rules-based building design, asset light manufacturing and predictive modeling to repeat processes and bring precision at scale, allowing the company to lower costs and be more sustainable. Juno uses a few dozen components for each project to efficiently repeat processes while also reduce errors and increase speed.
The install requirements are baked into the components to optimize construction time, and materials are delivered just in time to the project site. The Austin project displayed during SXSW was located in a tight urban location, yet the 5-story, 24-unit building was still assembled in 5 weeks with a crew of 5 people and the exterior curtain wall was assembled in only 16 days.
“What Juno is doing uniquely is the platform approach,” said Jonathan Scherr, founder and CEO at Juno. “We’re developing our own buildings to provide the concept, but we have the ability to scale because we can use the platform of a set of components. We’re light because we don’t own a factory. We can work with other developers across the country, with repeatability.”
From the sustainability lens, Juno designs using components of mass timber because it sequesters carbon and is renewable, so the buildings can be considered carbon banks that store carbon. Offsite fabrication also reduces waste.
Juno offers design, development, and management services and carefully and strategically has built relationships with suppliers and factories.
“If you are trying to scale, you cannot do that alone,” Scherr said. “You don’t scale with a single idea. We scale with an ecosystem of partners. We are a hub, instead of a typical highly fragmented process. Because we create direct relationships across each part of the development process, we can assemble a project a lot faster and be much more efficient.”
The company also wants to make sure contractors can work with suppliers to find the right materials that are being specified without relying on any one supplier exclusively.
“Juno helps construction teams on its projects source directly from suppliers across the U.S. and internationally,” he said. “And while we want to power a new way of building, we need to make sure we specify materials and parts that won’t be single sourced.”
From South America To Pittsburgh
After living in South America to create a documentary on housing design, Brian Gaudio returned to his home city of Pittsburgh with the burning desire to solve for affordable housing and launched his own company Module.
The company has had several breakthrough projects in collaboration with other groups invested in the mission and recently launched a Mission-Driven Developer Program that provides up to $25,000 in pre-development funding and technical support for developers working in disadvantaged communities to build affordable or workforce housing. The first developer has been selected and Module will select up to five more winners.
“We are looking to invest in projects that align with our mission and where we can make a significant impact,” said Module’s COO Marquis Cofer. “As the design firm for a developer, we can put some skin in the game early by providing design services like concept design, site planning, and zoning analysis.”
Construction on the first project starts this month and will be two homes located in Pittsburgh for the Amani Christian Community Development Corporation. Module consulted and designed the project and will serve as builder and general contractor. With its offsite efficiencies, the cost of the home leaving the factory will land at about $125 per square foot.
“It is a popular floor plan that we created for organizations building housing for 60 to 80% AMI (area median income) and not have to bring subsidies in,” Cofer said. “In the design process every square foot counts, so the design was very intentional.”
Energy efficiency is one of Module’s objectives, so the homes were designed to U.S. Department of Energy Zero Energy Ready standards that can later translate to lower energy bills. Cofer says that can equate to utility savings of about $1,000 per year.
“The goal for the program is to get homes built,” he said. “We know that modular homes are still a small percent year over year and are not widely adopted, known, or understood. Some builders had a less than ideal first experience with modular so they cannot overcome that and pursue a second project. We want to help resource strapped projects and make proof points. Our goal is to get people in the homes at affordable levels and as quickly as possible.”
Module’s goodness doesn’t stop there. The company is partnered with the Trade Institute of Pittsburgh to allow people to get hands on working experience on Module job sites and in the factory.
Even though the program has a finite budget, the hearts at Module are bottomless.
“Even if people don’t win in the challenge, we will keep doing this,” Cofer said. “Still apply or reach out, because we can probably still do something. We are not giving funds to everyone as a loan, but we want to work with as many as possible who are mission-aligned and figure out a way to work together.”
Developers in the program will have priority on Module’s manufacturing line to shorten cycle times for developers that are creating affordable homes where they are needed most.
A Competition
In the middle of the country, some modular construction enthusiasts have kicked off a competition to highlight the value of offsite construction for more affordability and innovation. They brainstormed the Gateway Decathlon to pit 11 teams from around the world against each other to design, assemble, and exhibit a housing project in October 2025 in St. Louis.
Then, some of the homes from the competition will be permanently relocated to the north side of the city to revitalize the area and provide families in need with a beautiful, efficient, and easy to maintain home.
The project developer, Good Developments Group, values this event as an opportunity to connect the housing industry with research institutions to address topics around future attainability, resiliency, and innovation. The company assembled a veteran team including Richard King, who was the founder of the U.S. Department of Energy Solar Decathlon and serves as the Gateway competition director, and Bobby Vance, who is an offsite industry subject matter expert and serves as the competition manager.
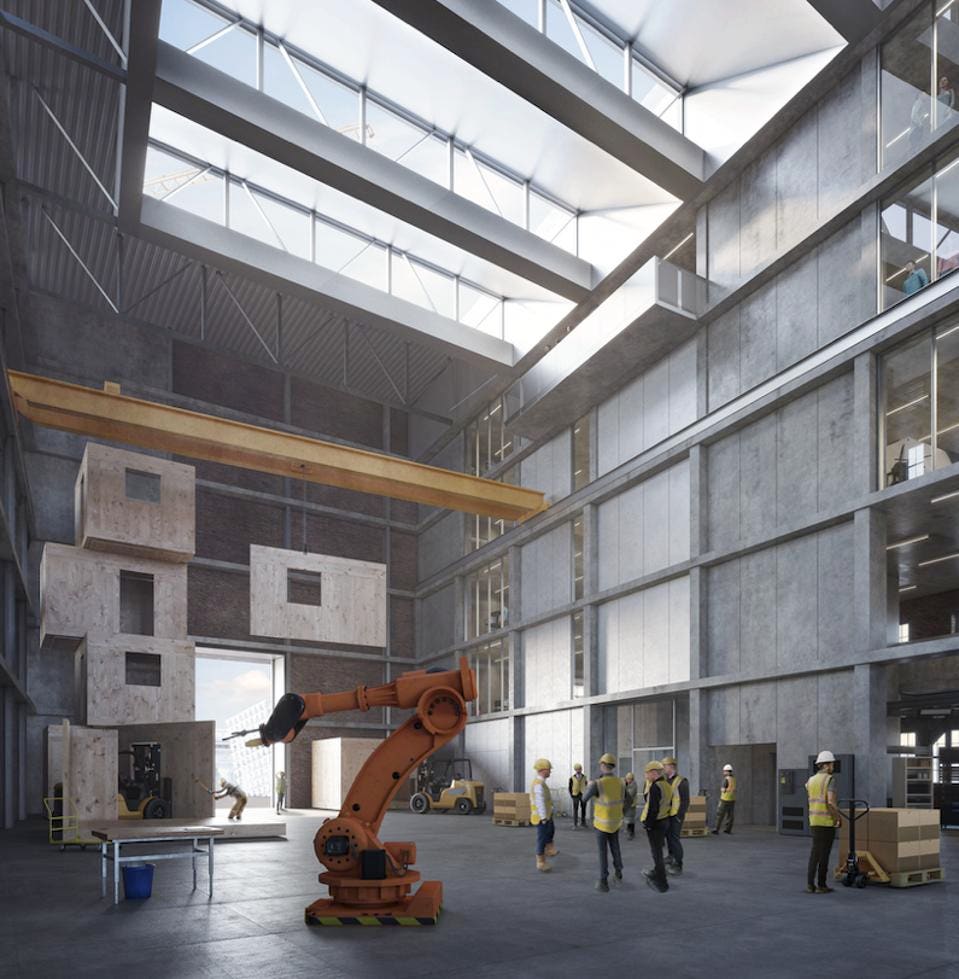
The Gateway Decathlon will roll into the just launched Gateway South, a geographic area dedicated to ongoing development of logistics, talent, and technology to improve construction productivity and performance. The first of its kind space will offer the industry the opportunity to change the supply chain, to streamline offsite construction, to adopt new materials and digital technologies, and to attract and train a new skilled workforce all while strengthening the St. Louis market.
The teams that are selected to participate in the decathlon will receive $100,000 in seed money to lay the foundation for their contributions to spotlight the benefits of offsite design, engineering, construction, and implementation over traditional onsite construction. Other factors will be considered a result of the new construction approach, including energy performance, functionality, and resource optimization.
Teams also will be graded on the scalability of the solution, taking in factors such as the transportation and logistics of getting product to a job site along with the speed and efficiency of the assembly and disassembly process.
Beating High Housing Costs
In California, the housing situation is more urgent than in other parts of the country and it’s where Steve Glenn’s B Corp certified company Plant Prefab launched a collaboration with non-profit Community Corporation of Santa Monica to build the Berkeley Station affordable housing development.
After years of experience with prefabrication and different go to market approaches, Plant Prefab found the sweet spot to scale, the process to reduce costs, and the partners to deliver the right design.
Plant Prefab leaned into the strong affordable housing architecture experience of Brooks + Scarpa to do the design, combining onsite construction with factory production to optimize time, labor, and materials. When complete, the Berkeley Station project will offer 13 units of 100% affordable housing for low-income families and transition-aged youth.
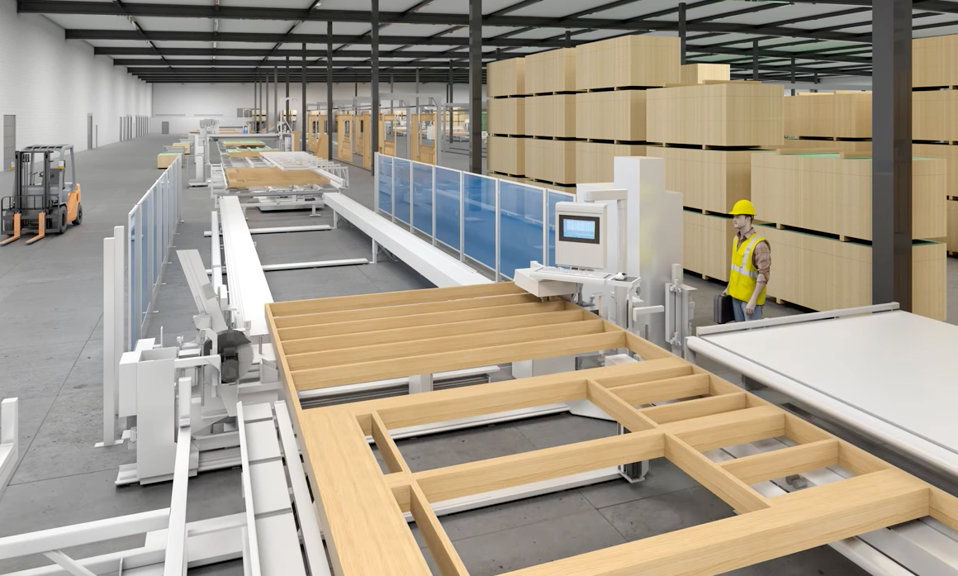
The 13 units will be built offsite in Plant Prefab’s new solar-powered, automated factory, minimizing carbon emissions and reducing material waste to less than 2%. The affordable housing project also is designed to meet LEED Gold standards with renewable energy and Energy Star appliances for more efficient performance.
A total of 24 modules will be used to complete the project. The modules will be built with panels manufactured on the automated line and then assembled in the same facility. Then, the modules are shipped to the site.
Glenn is checking all the boxes by offering sustainable, affordable housing in geography where it is a critical need.
“We just signed a contract for 60 unit 100% affordable housing project, so this is going to be a major focus for us,” he said. “And as the only automated facility in Southern California and the only high volume factory, we have lots of capacity and a great desire to help make a dent in affordable housing.”
Technology To Bring Investment
Another industry veteran, Chris Langford, managing partner at Home Technology Ventures, is stripping down the conversation on affordability to make room for innovation that his company, Home Technology Ventures, will fund. The firm’s four core beliefs drive its investment strategy for more attainable and sustainable housing.
First, a home is fundamental to the human experience, providing sanctuary, community, and pride. Second, innovation is a necessary component of change, so today’s housing challenges must be disrupted. Third, housing has arrived at an inflection point where current methods of building, transacting, financing, and caring for homes are unsustainable and exacerbating affordability and attainability. And, fourth, it is early in the technology adoption cycle that needs radical transformation and adoption of technology.
“What is unique is the thought that there is a total cost for being housed in America,” Langford said. “If you are a Section 8 voucher holder or you are upper class in a luxury neighborhood, both have costs and many of them are not embedded in your monthly rent or mortgage payment. Within the current inflationary environment, no matter where you sit, you are starting to feel the pinch and that is becoming tangible in a variety of ways.”
The firm is trying to come up with a different vision on how to think about that conversation and map activities to make housing more affordable for all people.
Langford has developed a framework using the acronym HOME to break down all the costs of housing. H stands for the cost of the house, and embedded in that is the cost of land, labor, materials, and regulatory compliance.
The O is how much it costs to occupy the home, and includes closing costs, inspections, repairs, cost of capital, down payment or deposit, moving costs, taxes, HOA, POA, and insurance. The M is for maintenance, repair, and improvements to the home for functionality, including paying utilities. These are ongoing cost burdens to compliment living in the housing.
And perhaps the most complicated is the E, for equity. Equity can be the offset of the other three since the asset can appreciate, but the process of getting access to that equity remains tricky especially for renters.
“The theory is that many of these costs are mitigated because I own an asset and I have equity in that asset, but there is high friction to accessing that equity,” Langford said. “HELOCs and cash-out refis, while allowing me to stay in my home, increase debt obligations to get access to my own asset. Selling my home to unlock my equity is both burdensome and laden with transaction costs. Despite this, we have concluded that renters’ cost of housing is more expensive because they have no equity, but these ancillary costs are rising at a rate that is making us question that dogma at a time when new innovations are allowing tenants to participate like an owner while acting like a renter.”
The HOME model recognizes the role different industries play in affordability. If we can reduce the costs of building a new home, then we can lower the burden associated with the cost of occupancy. If we upgrade our housing stock to become more resource efficient and resilient, we reduce utility costs and insurance premiums, and if homes become more intelligent, the annual cost of maintenance and improvements can be reduced.
Finally, by reducing the friction and the costs to access home equity, overall housing costs will be easier to manage.
So, Langford does the math. If it costs $40,000 to occupy a home on an annual basis, and the home appreciated $25,000 in that same year, and that money was available to the owner to offset those costs, then the net cost of housing would be $1,250 per month. Instead, housing costs remain at $40,000 while the $25,000 remains locked up until the owner takes action to unlock it and this deferral of benefits keeps many shut out of ownership.
“The goal is to deconstruct the three layers,” Langford summarizes. “If we can lower the first three and elevate equity, even taking it in subsets a homeowner could calculate their home score (HOME) and they may be doing directionally better than they thought they were.”
With innovations, such as prefab, Home Technology Ventures is investing in a future capable of these paradigm shifts.
A Future Of Hope
Many think that the automation of prefabrication is the future. I also believe the benefits associated with it have been proven, and that if we can bring it to scale and change industry culture dynamics, there is a huge runway for more and better housing.
Groups like the Advanced Building Construction Collaborative are paving that path by bringing together the right people and organizations to modernize and advance the process.
While some think that modular is hokey or unattainable, I disagree. Not only do I think it’s the right path, I think it’s being done with honor, passion, and bold moves, and that I admire.
The smartest construction companies in the industry already get their news from us.
If you want to be on the winning team, you need to know what they know.
Our library of marketing materials is tailored to help construction firms like yours. Use it to benchmark your performance, identify opportunities, stay up-to-date on trends, and make strategic business decisions.
Join Our Community