Prefabrication in Construction: A Cautious Look at a Promising Future
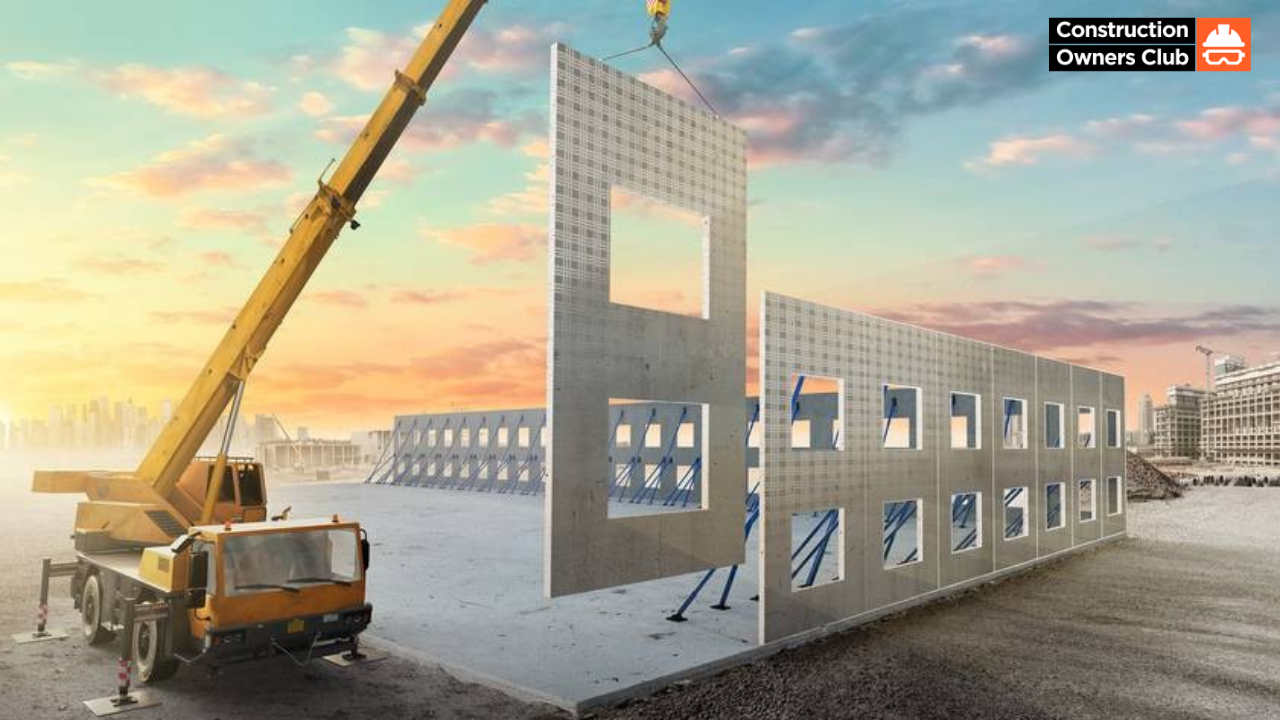
The construction industry faces a growing demand for efficiency, productivity, and cost-effectiveness in an ever-changing landscape. Prefabrication emerges as a potential solution, but its adoption requires careful consideration.
Traditional methods, while reliable, struggle to meet these stringent demands. Rising costs, sustainability concerns, and skilled labor shortages add further pressure. While prefabrication offers a way to address these challenges simultaneously, it necessitates a cultural shift within the industry.
Benefits and Considerations
Prefabrication offers several advantages:
- Increased Efficiency and Productivity: Shifting construction activities to controlled factory settings allows for greater control over costs, scheduling, and risk mitigation. Parallel processing of tasks can significantly reduce building time.
- Improved Quality and Sustainability: Digital tools and advanced logistics enhance the quality and efficiency of prefabricated structures. Prefabrication often uses less material and reduces waste on-site, aligning with sustainability goals.
There are, however, challenges to consider:
- Mindset Shift: Prefabrication requires a move away from traditional methods and an embrace of collaboration, innovation, and a willingness to challenge established norms.
- Collaboration is Key: Effective prefabrication necessitates collaboration across disciplines to optimize jobsite safety, minimize waste, and maximize efficiencies.
- Early Planning and Expertise: General contractors must be proactive in educating themselves and their teams on prefabrication. Project teams and developers need to embrace a paradigm shift, integrating prefabrication into the project strategy from the outset. This includes early collaboration, design decisions, and continuous cost estimating aligned with target value design.
Becoming a Prefabrication Champion
General contractors can play a pivotal role in driving the adoption of prefabrication by following these steps:
- Develop Internal Expertise: Designate champions to foster a culture that understands the benefits of prefabrication.
- Educate Yourself: Research and visit prefabricators in your region to understand product offerings and identify their best use cases.
- Evaluate Project Suitability: Assess past projects for areas where prefabrication could have improved outcomes. Identify repetitive elements like facades, MEP systems, and structural components as potential candidates.
- Plan for the Future: Identify upcoming projects that could benefit from prefabrication and consider if your team is equipped to lead a prefabrication strategy.
Prefabrication is Not a Universal Solution
While prefabrication offers numerous benefits, it's not suitable for every project. Projects in the late design phase, lacking repetition, or with complex architectural features might not be ideal candidates.
General contractors must be able to effectively communicate the suitability (or lack thereof) of prefabrication for specific projects. When a project isn't a good fit, suggesting alternative solutions to achieve similar goals demonstrates a commitment to client success.
Conclusion
Prefabrication presents a promising path toward a more efficient, productive, and sustainable construction industry. However, a cautious and thoughtful approach is crucial for successful implementation. General contractors who embrace prefabrication while acknowledging its limitations will be well-positioned to deliver superior results and value to their clients in this evolving landscape.
The smartest construction companies in the industry already get their news from us.
If you want to be on the winning team, you need to know what they know.
Our library of marketing materials is tailored to help construction firms like yours. Use it to benchmark your performance, identify opportunities, stay up-to-date on trends, and make strategic business decisions.
Join Our Community