Suffolk Enhances Steel Tracking with Proprietary BIM-Based Tech
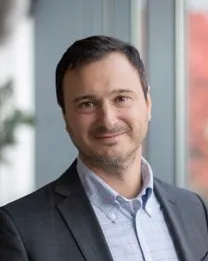
For Suffolk Construction, managing the complexities of structural steel erection is more than just good planning — it’s a tech-enabled strategy. The Boston-based contractor is using a proprietary tool, Live Dimensions, to simplify and standardize how steel progress is tracked across its projects.
Developed in-house by Suffolk’s Director of Digital Engineering, Denis Leff, the platform bridges the gap between complex building models and on-the-ground construction realities. At its core, Live Dimensions is designed to catch the details that often get lost in translation — where a single misplaced beam can delay or compromise a project.
Unlike conventional approaches — which often rely on manual data input via spreadsheets or siloed tracking systems — Live Dimensions integrates directly with BIM models. “BIM models hold all the information of what we’re about to build,” Leff said. “And I see them generally as underleveraged in our industry, partially because the technology blocks a lot of people. They don’t know how to access the data unless you’re a BIM expert.”
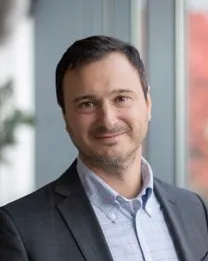
Bringing BIM to the Jobsite
The system’s core value lies in how it uses artificial intelligence to parse and unify project datasets into a dynamic, real-time BIM interface. This not only enhances transparency but also provides immediate insights into the status of every piece of steel — from design to fabrication and final installation.
The platform is currently in use at Suffolk’s South Shore University Hospital Pavilion Core & Shell project in Bay Shore, New York. The first phase of the $468 million development includes demolition, utilities, and a full core and shell. The team celebrated its steel topping out last October, with completion expected by Q2 2026.
There, the tool has proven particularly helpful in resolving two persistent pain points: delivery tracking and completion verification. Instead of juggling multiple Excel files or investing in expensive third-party platforms, the team simply uploads a BIM model into Live Dimensions, tags it for tracking, and scans in delivery documentation like bills of lading to keep the system updated.
“Knowing where the material is and what state it is in to ensure continuity in the field is really important, because you don’t just stop steel if the steel isn’t ready. You stop the entire project,” Leff said.
Tracking the Routine — and the Unexpected
While still relatively new, the tool has already helped Suffolk flag common jobsite disruptions, including bolt hole misalignments and damaged beams. “A lot of this stuff is par for the course. It happens on every project,” said Leff. “But we’re really trying to get an understanding — is it a project in New York? Is it a particular contractor? Is it a particular fabricator? Is this going to happen, more or less, with certain people that we partner with?”
Although it’s too early to measure the tool’s effectiveness in reducing rework, its ability to collect and contextualize data has been a game changer in understanding recurring issues and potential trends across builds.
Built In-House, By Builders
Leff’s journey toward building Live Dimensions began overseas. He spent six years working for Samsung’s construction division in South Korea, an experience that deepened his appreciation for high-efficiency BIM systems. “Here, I’m able to understand the project’s needs at a comfortable pace, try things out, reiterate, improve,” he said. “It’s not like being an external person trying to create a solution for someone else. You have a little bit more time to do things thoughtfully, and that’s why I’m going one project at a time.”
He developed Live Dimensions in just six months, ahead of the South Shore project’s steel erection. With support from digital engineering intern Matthew Chen, Leff transitioned the tool from a standalone app to a more robust, web-based platform.
Suffolk’s innovation-friendly culture played a major role in the project’s success. The company operates its own venture capital arm — Suffolk Ventures — aimed at advancing construction tech throughout the building process.
“We’re very tech-forward as an organization, so there’s a lot of support for reaching our goals, our passions, if they fit the bill of moving our company forward,” Leff said.
Originally reported by Matthew Thibault in Construction Dive.
The smartest construction companies in the industry already get their news from us.
If you want to be on the winning team, you need to know what they know.
Our library of marketing materials is tailored to help construction firms like yours. Use it to benchmark your performance, identify opportunities, stay up-to-date on trends, and make strategic business decisions.
Join Our Community