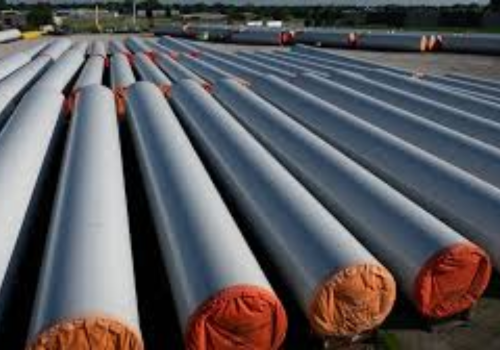
Tariff Uncertainty Clouds Construction Costs as Contractors Adapt
As tariff hikes loom, construction contractors are bracing for continued price swings and supply chain headaches that could stretch into next year.
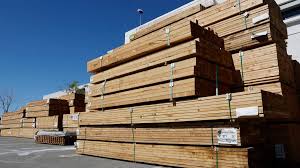
Construction input costs rose 6% through May compared to last year and remain more than 40% above pre-pandemic levels, according to the U.S. Bureau of Labor Statistics. The increases come amid policy back-and-forth that has left contractors scrambling to adjust procurement strategies.
“The impact of tariffs will impact not just the price, or cost, but also the quantity consumed of such goods,” said Michael Guckes, chief economist at ConstructConnect. “The fact that many tariffs have been delayed, some several times now, may mean that more inflationary pain is to come.”
For many contractors, the uncertainty is already creating real-world setbacks. Unistress Corp., a Massachusetts-based precast manufacturer, laid off 233 workers after two major projects stalled over steel price fluctuations.
“Given the current landscape, we anticipate continued volatility in materials pricing through the second half of the year,” said Michael O’Reilly, vice president at Rider Levett Bucknall. “A meaningful decline in costs appears unlikely without greater clarity or stabilization in trade dynamics.”
President Donald Trump’s administration suspended several country-specific duties earlier this year, then reversed course, announcing in July that tariffs would resume Aug. 1 for nations lacking trade deals. Key materials — including rebar, structural steel, copper, and aluminum — are directly affected.
Contractors like Swinerton are countering these swings by pivoting to alternatives like mass timber. “These strategies should be transparent and developed in close collaboration with project owners to proactively manage risk,” said O’Reilly.
Meanwhile, Timberlab’s push for a vertically integrated supply chain — with a sawmill coming online in 2027 — aims to limit dependence on volatile imports. But workforce constraints remain a bottleneck.
“Our labor force is neither skilled up for, nor physically large enough and with sufficient free capacity, to produce the types and volumes of goods we currently import,” said Guckes.
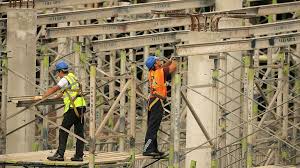
As the industry eyes the second half of 2025, experts say macroeconomic factors and trade clarity will determine whether project pipelines stay resilient — or stall.
“While recent tariff activity has certainly been a factor, it hasn’t been the primary driver of construction trends in 2025,” said O’Reilly. “Looking ahead, construction activity in the second half of the year will likely be shaped more by macroeconomic forces than by tariffs alone.
Industry analysts say contractors are seeking new ways to hedge risk. Some firms are locking in bulk orders for critical materials well in advance or storing supplies near job sites. Others are negotiating escalation clauses into contracts to share cost surges with project owners.
Meanwhile, private developers are increasingly cautious. Data from ConstructConnect shows a sharp 62.6% spike in private project cancellations in May alone — the highest monthly total on record.
Labor shortages add another wrinkle. Even if more factories come online to boost domestic production, the lack of skilled tradespeople could slow output. That raises fears of stagflation — slowing demand coupled with persistent inflation — that may extend into 2026.
Contractors and owners alike are watching policy developments closely. Should tariffs stay in place without clear trade deals, more firms may double down on alternative materials and local sourcing to cushion future shocks.
Originally reported by Sebastian Obando in Construction Dive.
The smartest construction companies in the industry already get their news from us.
If you want to be on the winning team, you need to know what they know.
Our library of marketing materials is tailored to help construction firms like yours. Use it to benchmark your performance, identify opportunities, stay up-to-date on trends, and make strategic business decisions.
Join Our Community