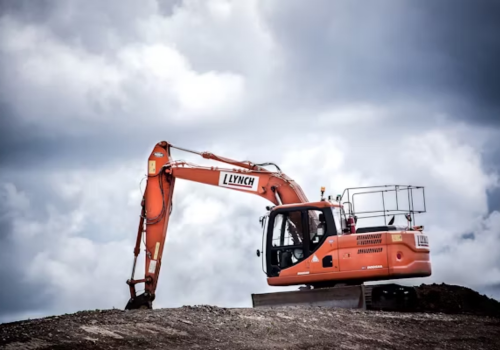
BALTIMORE - According to Hannu Lindberg, technology leader at DPR Construction, construction project owners adopting digital twin technology can not only unlock immediate value but also influence the future of project building, management, and maintenance. Speaking at the National Institute of Building Sciences Digital Twins conference, Lindberg highlighted that digital twins—one of the most transformative and underutilized technologies of our time—are vital for optimizing, modeling, and enhancing buildings, products, services, and processes.
"Digital twin technology is transforming the design and construction of a building from its traditional, fragmented approach into a collaborative, data-driven process," Lindberg stated.
"The use of the technology enables greater prototyping in design, facilitates digital workflows for prefabrication and robotics integration, mitigates field rework, improves quality, and allows owners to have a virtual representation of real-world entities to maintain their assets with greater accuracy."
By integrating digital twins, owners can lay the groundwork for innovative, resilient, and sustainable lifecycle asset management, generating long-term value. Lindberg shared five key reasons why owners should embrace this technology:
Enhanced Project Visibility and Control
Digital twins offer an accurate digital replica of a building, allowing owners to interact with their property virtually, detect potential issues, and make informed decisions to improve building operations. This visibility ensures projects stay on track and helps prevent costly retrofits after project completion.
Cost Savings Through Efficiency
Using data sources such as laser scans and point clouds, digital twins reduce inefficiencies, prevent expensive rework, and optimize material usage, while collaborative delivery methods eliminate redundant efforts in 3D modeling.
Improved Sustainability
Digital twins help create lean processes and energy-efficient designs, contributing to sustainability goals by tracking energy usage and reducing material waste, leading to greener operations and smaller carbon footprints.
Streamlined Maintenance and Operations
Once construction is complete, digital twins act as dynamic as-built records, simplifying facility management. Owners can leverage these models for predictive maintenance, reducing downtime, and ensuring smooth renovations and expansions.
Improved Tenant Experience and Lifecycle Savings
By boosting maintenance productivity and maximizing facility uptime, digital twins enhance tenant satisfaction and offer significant lifecycle savings.
Lindberg emphasized that the most effective digital twins are created in close collaboration with architects, engineers, contractors, and trade partners during construction. "This collaboration is facilitated through alternative delivery methods, including progressive design-build or integrated project delivery workflows, early contractor involvement, and precise logistics planning," he said.
About DPR Construction
DPR Construction is a leading self-performing general contractor and construction manager specializing in technically complex and sustainable projects across various sectors, including advanced technology, life sciences, healthcare, and education. Founded in 1990, DPR has grown into a multi-billion-dollar organization with a global presence, focusing on delivering predictable outcomes through virtual design, prefabrication, and data-driven insights. For more information, visit DPR Construction.